Article Index
Foil ConstructionBy: Astor Universal
Reprinted from Hot Stamp News
Issue: Fall 1998
As always the API Group foil companies', is to educate our customers. The more you know
about foil and it's application, the better we can serve you. The following
information will give you an overview of the construction of foil, which is
intended to help you to understand why we recommend specific application techniques, and
different grades of foil for different applications.
There are five standard layers which make up the foil "sandwich".
Layer # 1: Polyester film
Clear polyester film in roll form is used as the carrier for the different layers of
foil. A 1/2 mil or 50-gauge film is the most commonly used carrier. Currently, polyester
is the optimum film, for the following reasons:
- Resists punctures from the die
- Smooth, reflective surface
- Very thin, allowing for optimum roll lengths
- Quick heat transfer
- Flat profile to ensure even transfer of coatings
- Resists heat of die without wrinkling or melting
Layer #2: Release coat
This coat causes the other foil layers to release from the polyester film carrier when
heated by the die. It is applied as a solvent solution, a mixture of waxes or resins
chosen specifically for the highspeed releases required today. The precision needed to
apply this layer is often underestimated and typically, is what sets foil manufacturers
apart. Invisible cratering can occur if the release coat isn't properly applied and this
can play a major role in the inconsistency of hot stamping foils, if not properly
monitored.
Layer #3: Lacquer coat (color coat)
The lacquer coat is the color layer through which the next metallized (mirror-bright
aluminum) layer is viewed on the finished foil stamped substrate. The lacquer coat:
- Carries the color in the form of dyes or pigments
- Determines the scuff/abrasion resistance of the foil
- Determines the chemical resistance of the foil
- Must be brittle enough to give sharp definition to the foil stamped image
- Must be transparent or translucent to achieve the proper metallic finish
In the manufacturing process, the lacquer coat must be applied by a very consistent
coating system, as it will dictate the specific foil color and contribute to the stamping
performance of the product.
Layer #4: Metal coat
The metal coat, generally aluminum, gives reflectivity and opacity to the foil product.
Before it can be applied to the film, the aluminum is vaporized through a combination of
heat (1800' F) and vacuum, in the process known as vacuummetallization. The aluminum
condenses on the color coat to form an extremely thin, mirrorbright metallized coating and
is then quickly cooled by a chilled roller to prevent the polyester film from melting.
|
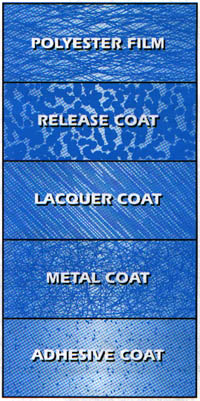 |
Layer #5: Adhesive coat
The adhesive or "size coat" serves to bond the foil to the substrate being
stamped. The adhesive is a mixture of low melting point resins, which melt at the stamping
temperature to form a chemical or physical bond with the stamped surface. That bond must
obviously be greater than the bond between the release coat and polyester film to ensure a
successful imprint transfer. The printability characteristics of a foil are primarily
determined by this coat. The greater the amount of size or adhesive, the more bonding and
heavier coverage the foil will demonstrate.
Article Index